|
Where do sparkling stamps come from?
California Clear Stamp was founded in 2006 for the purpose of
producing high quality photopolymer products. The founders have
all had extensive experience
in the flexographic printing plate or hand stamp manufacturing
business. When an existing photopolymer printing plate manufacturing
facility became available,
they felt it provided a perfect operation to produce clear stamps
for the hobby and scrapbooking markets. The facility contained
a modern large format processing
line that was modified into a high volume polymerization process
producing “sparkling” clear stamps.
Using advanced resins and manufacturing techniques,
the “sparkling” clear
stamp was developed. It offers outstanding ink transfer characteristics,
resists yellowing,
and has improved tensile strength for tear resistance.
Genuine photopolymer hand stamps, unlike silicon or vinyl stamps,
owe their outstanding ink transfer characteristics to their heritage
of development in the flexograhic
printing plate industry. The photopolymer resins were originally
developed in the printing industry as a replacement for the hand
engraved or molded rubber-printing
plates being used. Their manufacturing process and ink transfer
characteristics were improved until they became the preferred
printing plate, replacing rubber, for
most flexographic printing processes worldwide. Now, after 50
years of development, the modern resins (offering outstanding
ink transfer and ease of use for the art
stamp hobbyist) have become a recognized alternative to rubber
in hand stamping.
Clear stamps are now produced in photopolymer, silicon, and
vinyl materials. However, only photopolymer has the microscopic
porosity, developed for the printing
industry, necessary for excellent ink transfer. The silicon and
vinyl materials have a non-porous, slick surface, which has difficulty
in even ink transfer. Insist on genuine
photopolymer for the ultimate in clear stamps.
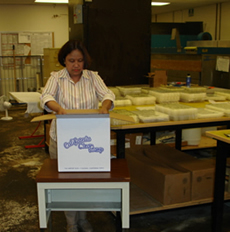
Packaging
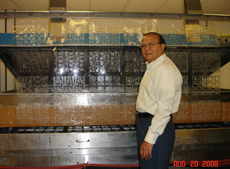
Postexposure Station
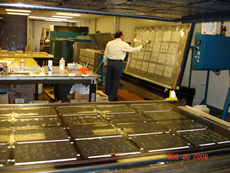
Reclaim looking thru Exposure Station |
Manufacturing
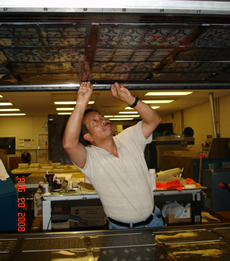
Placing Negatives
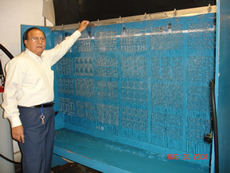
Final Rinse
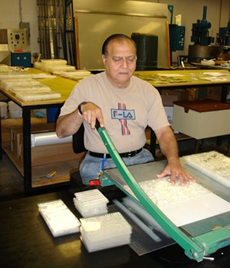
Final Trimming
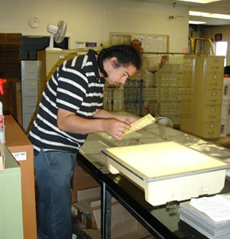
Inspection
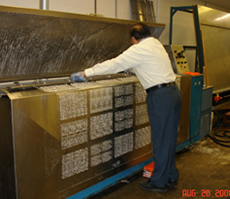
Washout Station
|
|